WELDING FOR THE CLEAN ROOM
Welding for cleanrooms is an important part of our daily work. Our customers develop or produce high-precision, high-tech applications that are manufactured under cleanroom conditions. Highly sensitive technology, such as in the semiconductor industry, must be protected from contamination by means of professional welding. Even the smallest particles are enough to disrupt the function or impair precision. This is a scenario that our customers in the optics and precision mechanics sectors in particular want to avoid. We achieve this primarily through weld seams with the smoothest possible surfaces.
For our "cleanroom customers", we mainly weld devices or racks that are used for development or production in cleanrooms - or as mobile systems for transporting heavy weights from one cleanroom to another. For this purpose, they also have to be prepared, cleaned, assembled and made ready for transportation in the cleanroom. FRITZ is prepared for this - we also offer the complete process chain "around it".
CLEANROOM WELDING AT A GLANCE
The highlight: We cover all processes beyond the welding process!
- In advance on request: cleanroom-compatible engineering or parts production
- Procurement of the right cleanroom-compatible materials
- Cleanroom-compatible MIG/MAG welding work with surfaces that are as smooth as possible,
- From batch size 1, also larger racks
- Cleaning in the cleanroom under UV light, including wipe test with "lint cloth"
- Clean room packaging and delivery
- All parts that pass through cleanrooms are documented
- For flanges or containers: with tightness and leakage test
- On request: Weld seam testing and documentation by an accredited testing laboratory
CLEANROOM WELDING IN DETAIL
A certain "roughness" cannot be avoided during welding. Nevertheless, welding beads must be "smooth" for cleanroom requirements. How do we achieve this? It's a combination of experience and craftsmanship. We make sure that we keep the pores as small as possible. Afterwards, most parts are stripped with a layer of paint. This cleans the pores.
This is followed by testing and then cleaning in the clean room. Even the last particles are removed under UV light. We have the necessary equipment for this purpose, such as special cloths for the wipe test. The welding surfaces must also be so "smooth" and clean that they pass the wipe test. In other words: that no lint is deposited on the seams when wiping. In cleanroom packaging, each part is packed at least twice. As we often have large parts, large tarpaulins are also welded together. As you can see: We do everything we can to keep particles out.
THE PUREST WELDING PARTNER FOR EVERYTHING
As mentioned, we cover all processes relating to welding. On request, from cleanroom-compatible engineering to cleaning and cleanroom packaging. We thus offer our customers the opportunity to have one contact partner for everything as a "single source". It starts with the procurement of the right cleanroom-compatible materials and does not end with leak testing, if required.
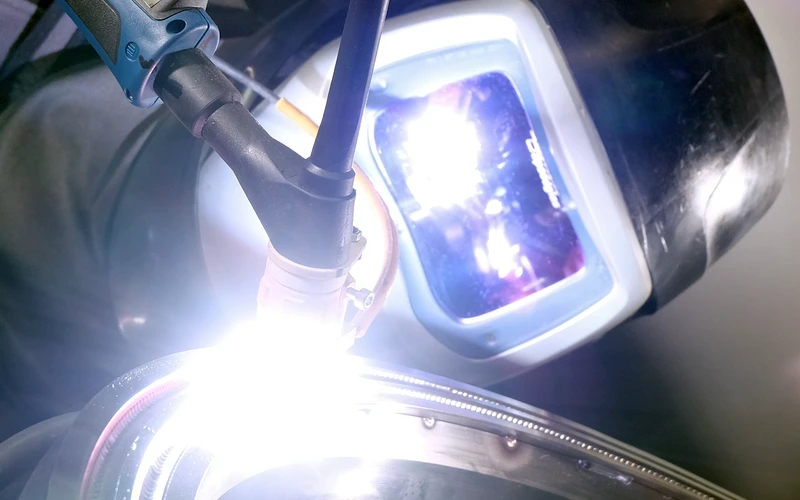
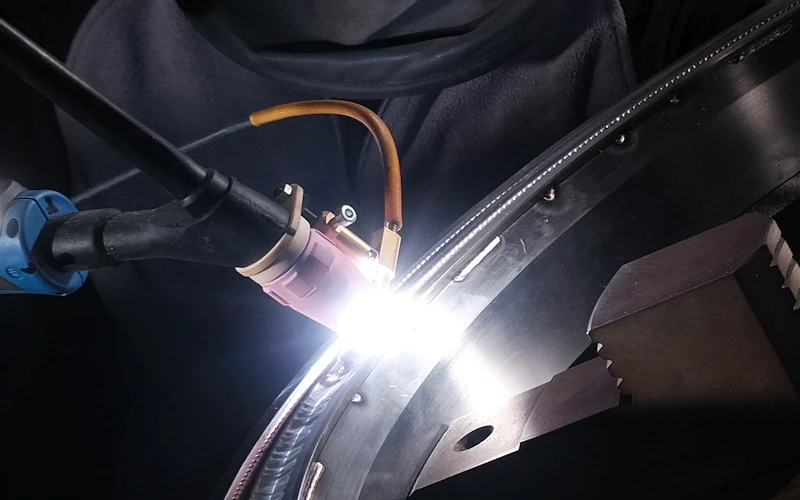
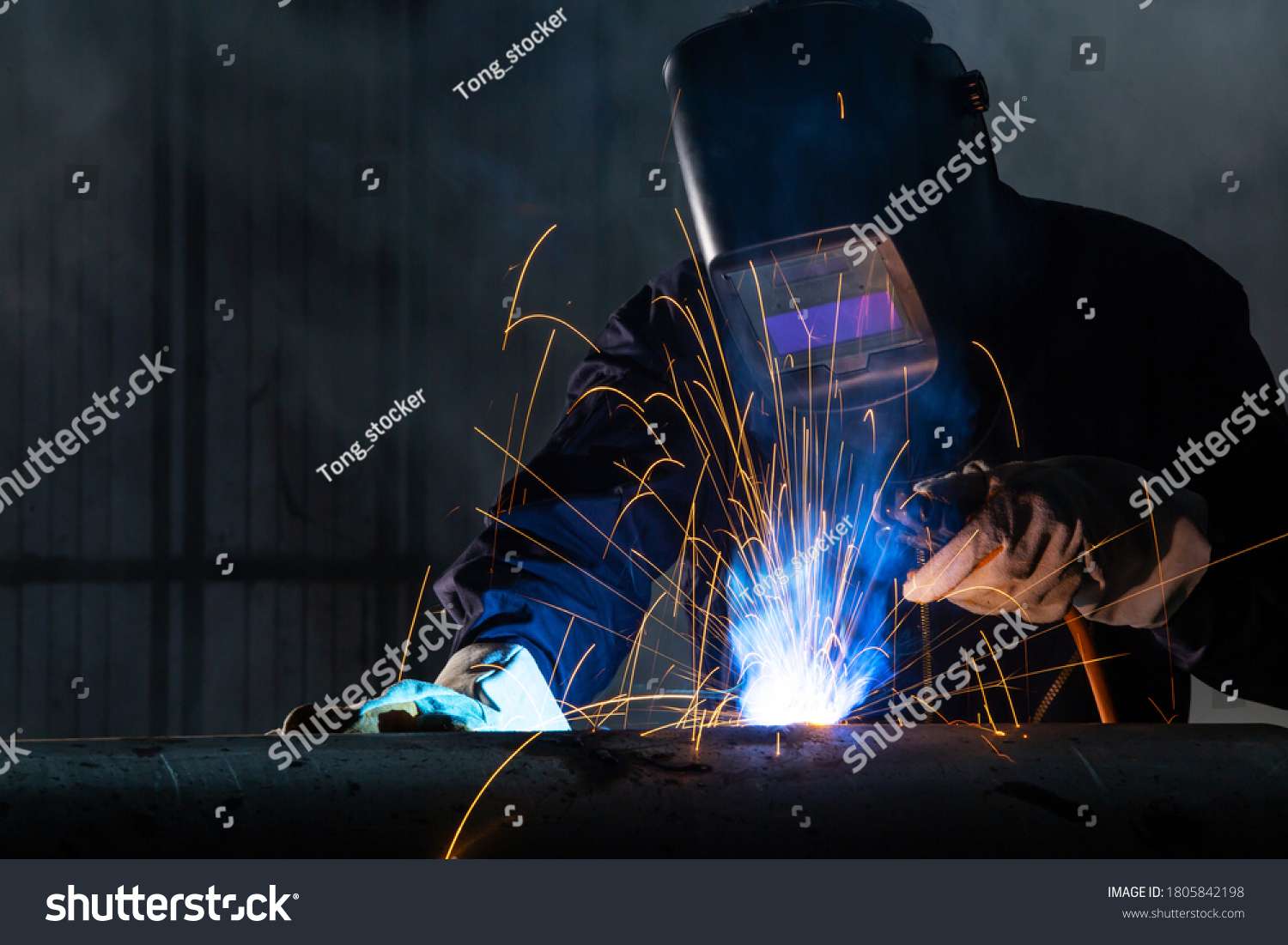
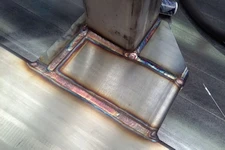
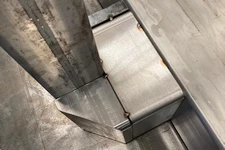
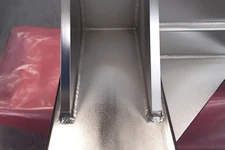
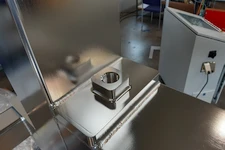
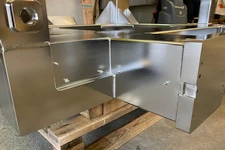
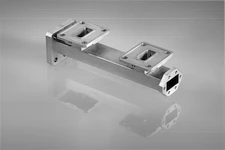