LEAK TESTING SYSTEMS IN A WATER BATH: BUBBLE TEST
Leak test systems or test chambers in a water bath, such as with bubble test, are available from FRITZ as special machines or as a more or less modified standard version. We offer: Test chambers for leak testing via negative pressure testing and test chambers for leak testing via positive pressure testing, for example for vacuum-packed or thermoformed products.
SERVICES AT A GLANCE
- Test chambers for leak testing via negative pressure test
- Test chambers for leak tests via overpressure testing (for vacuum-packed or thermoformed products)
- Testing, preliminary tests and validation
- Specifications, engineering and consulting
- Commissioning and training on site
- Support, maintenance, service, documentation, certification & more
LEAK TESTING MACHINE FOR LEAK TESTING VIA NEGATIVE PRESSURE
During the vacuum test, the test chamber is filled with water, the test product is inserted and the lid is closed. The product is pressed below the water surface by the integrated hold-down device and the air space above it is evacuated using the Venturi principle. As a result of the negative pressure, the air in the packaging expands and appears as visible air bubbles at leaks. This leak test not only shows you whether your packaging is leaking, but also where.
LEAK TESTING MACHINE FOR LEAK TESTING VIA OVERPRESSURE
In the overpressure test, the test specimen is placed in the water-filled test chamber with an adapter and filled with compressed air. Due to the overpressure in the test specimen, the air escapes at leaks and visibly bubbles upwards. This test method is particularly suitable for vacuum-packed or thermoformed products.
Example reference: Leak test with bubble test
Bubble test chamber BETty 42 + 240
- Different chamber sizes on request
- For example 400 x 300 x 350 mm (WxDxH), 890 x 600 x 450 mm (WxDxH)
- Limit leakage rate 1x10-4 mbar l/s
- Overpressure up to 8 bar (rel.)
- Vacuum up to 200 mbar abs. (- 800 mbar to ambient pressure), adjustable
- Vacuum generation using the Venturi principle
- ASTM module with fine regulator, sensitivity >0.2 mbar, display range 0-100 mbar
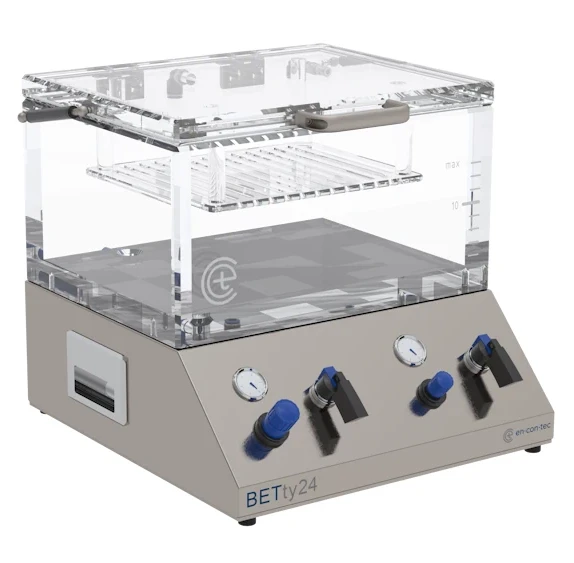